第5回 接着剤の選定、評価方法
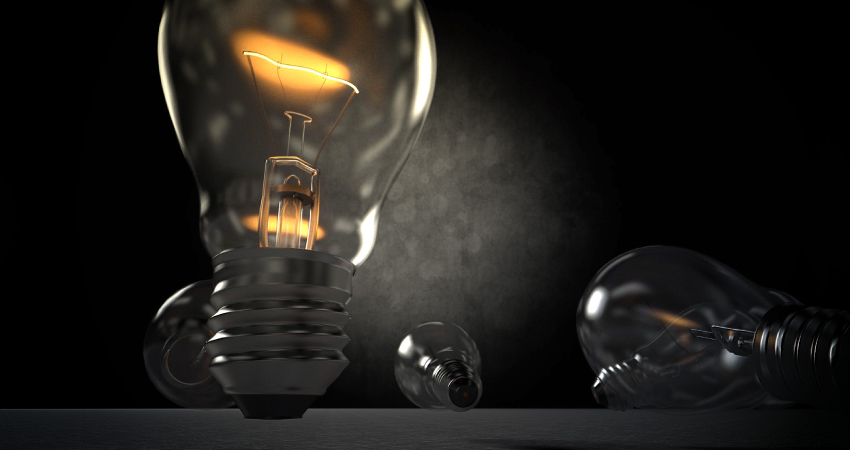
「接着ゼミ」第5回は、接着剤の選定、および評価方法について説明します。
1. 接着剤の選び方
1-1. 被着材料の組合せから選ぶ方法
最も簡単な選び方は、接着剤メーカーの総合カタログなどに掲載されている駅間料金表のような二種類の被着材料の組合せから適用可能な接着剤の種類を絞り込む方法です。
この方法は、どのような種類の接着剤が適用可能かを知る目安にはなりますが、そのメーカーが扱っていない接着剤は含まれないことも多いので注意が必要です。
1-2. 接着剤メーカーへの相談は後回しに
接着剤の選定に当たっては、接着剤メーカーに相談することが多いでしょう。 相談を受けた接着剤メーカーは、要求された機能や性能を満たすと思われる接着剤を紹介してくれますが、それが最適とは言えません。全ての種類の接着剤を扱っている接着剤メーカーは多くないので、自社で扱っている接着剤の中からしか候補品を紹介してくれないためです。メーカーは「この用途なら、うちの接着剤より他社の接着剤でより適切な物がありますよ」と親切な対応はしてくれません。
また、自社の接着剤の長所は説明してくれますが、欠点についてはあまり説明をしてくれません。ある程度検討が進み、評価を始めたり試作を始めた段階で、欠点による課題が表面化して、接着剤の選定が振り出しに戻ることは良くあることです。筆者は接着剤を製品組立に適用する立場の技術者であったので、何度となくこのような経験をした事がありました。
1-3. 欠点の少ないものを選ぶ
接着剤を選ぶ時の基準として、要求される機能や特性を満足するかどうかは重要です。一般に、接着剤の選定はこの観点から行われています。
しかし、接着剤は、第4回で述べたように、種類ごとに固有の多くの欠点も有しています。接着の不良は、接着剤の欠点に起因することが多いことを考えると、接着剤の選定時には、欠点の少ないものを選ぶことが極めて大切ということになります。
1-4. 欠点から候補接着剤の種類を絞り込むチェックリスト
そこで、接着剤を用いる立場で、接着剤メーカーに相談する前に候補となる接着剤の種類を絞り込むために筆者が作成したのが「消去法による接着剤の選定チェックリスト」です。表5-1に示しました。
この表は、上から、光硬化型、嫌気性、一液型変成シリコーン系、一液型シリコーン系、一液型ウレタン系などの湿気硬化型、瞬間接着剤、両面テープ、二液型ウレタン系、二液型エポキシ系、一液型エポキシ系、二液型アクリル系(SGA)、二液型シリコーン系と並んでいます。この表のチェック項目を上から順に質問に従ってチェックしていきます。その結果、判定が×になれば、次の接着剤に移ってチェックを続けます。判定で×が出なかった接着剤が候補接着剤となります。
表5-1 光硬化型接着剤の形態、反応機構、長所・短所
接着剤の種類 | 順番 | チェック項目 | 判定○ | 判定× | 適用可否・代替品 | 判定結果 | |
---|---|---|---|---|---|---|---|
光硬化型接着剤 | 共通 | 1 | 接着部に光を照射可能か | 可能 | 不可能 | →×なら適用不可 | |
2 | 油面接着性は必須か | ではない | 必須 | →×なら適用不可 | |||
3 | 部品はUVを透過するか | ではない | 必須 | →×なら適用不可 | |||
4 | 光が当たらない部分に接着剤が流れ込むことはないか | ない | ある | →×なら光・熱併用硬化型、 または、流れ込み防止対策検討△ | |||
可視光硬化型 | 1 | 部品は可視光を透過するか | する | しない | →×なら適用不可 | ||
光・熱併用硬化型 | 1 | 加熱硬化は可能か | 可能 | 不可 | →×なら適用不可 | ||
嫌気性接着剤 | 共通 | 1 | 接着層厚さが0.1mm以上になる部分はないか | ない | ある | →×なら適用不可 | |
2 | 不活性材料の接着でアクチベーターの併用は可能か | 可能 | 不可能 | →×なら適用不可 | |||
3 | 被着材表面はポーラスでないか | ではない | ポーラス | →×なら適用不可 (不明な場合はテスト要)△ | |||
4 | 油面接着性は必須では無いか | ではない | 必須 | →×なら適用不可 | |||
5 | 洗浄剤の残渣による硬化不良の心配はないか | ない | ある | →×なら適用不可 (不明な場合はテスト要)△ | |||
6 | はみ出し部は硬化しないが、はみ出し防止対策は可能か | 可能 | 不可能 | →×なら嫌気・UV併用タイプ または、はみ出し防止対策検討△ | |||
7 | 貼り合せ時の空気の巻き込み対策は可能か | 可能 | 不可能 | →×なら適用不可 | |||
8 | 硬化速度は接着層が厚くなると遅くなるが問題ないか | ない | ある | →×ならテスト要△ | |||
9 | 十分な強度を出すには加熱が必要だが加熱可能か | 可能 | 不可能 | →×なら室温硬化での強度で十分か確認△ | |||
嫌気・UV併用タイプ | 1 | はみ出し部のUV照射は可能か | 可能 | 不可能 | →×なら適用不可 | ||
湿気硬化型接着剤 1液弾性変成シリコーン系 1液シリコーン系 1液ウレタン系 | 共通 | 1 | 接着部に空気中の水分は十分に供給されるか | される | されにくい | →×なら適用不可 | |
2 | 接着作業場・養生場所の湿度管理は可能か | 可能 | 不可能 | →×なら適用不可 または、対策検討△ | |||
3 | 油面接着性は必須では無いか | ではない | 必須 | →×なら適用不可 | |||
弾性変成 シリコーン系 | 1 | 接着剤が柔らかくても問題ないか | 問題ない | 問題あり | →×なら適用不可 | ||
2 | 高温下での接着強度は低いが問題ないか | 問題ない | 問題あり | →×なら適用不可 | |||
1液シリコーン系 | 1 | 硬化中の発生ガスによる問題はないか | ない | ある | →×なら適用不可 | ||
2 | 接着剤が柔らかくても問題ないか | ない | ある | →×なら適用不可 | |||
3 | 後工程での問題(はじきなど)は無いか | ない | ある | →×なら適用不可 | |||
瞬間接着剤 | 1 | 接着面は小さいか | 小さい | 大きい | →×なら適用不可 | ||
2 | 接着層厚さが0.1mm以上になる部分はないか | ない | ある | →×なら適用不可 | |||
3 | 油面接着性は必須では無いか | ではない | 必須 | →×なら適用不可 | |||
4 | 接着部周辺の白化は問題ないか | ない | ある | →×なら適用不可 または、UV併用型瞬間接着剤 | |||
5 | はみ出し部は硬化しにくいが問題ないか | ない | ある | →×なら適用不可 または、はみ出し防止対策検討△ または、UV併用型瞬間接着剤 | |||
6 | プラスチックの溶剤によるクレージングは問題ないか | ない | ある | →×なら適用不可 または、はみ出し防止対策検討 または、UV併用型瞬間接着剤 | |||
UV併用型瞬間接着剤 | 1 | はみ出し部にUV照射は可能か | 可能 | 不可能 | →×なら適用不可 | ||
両面テープ | 1 | 油面接着性は必須では無いか | ではない | 必須 | →×なら適用不可 | ||
2 | テープ厚さと部品クリアランスの関係に問題は無いか | ない | ある | →×なら適用不可 または、部品精度見直し△ | |||
3 | 保持力(クリープ)、スプリングバック力による問題は無いか | ではない | 必須 | →×なら適用不可 または、他の接合法の併用検討△ | |||
4 | 低温ではタック性が低下するが作業に問題は無いか | ない | ある | →×なら適用不可 または、貼付け面の加温検討△ | |||
5 | 貼付け後に加圧は可能か | 可能 | 不可能 | →×なら適用不可 | |||
2液ウレタン | 1 | 湿度による発泡対策は可能か (作業環境、混合作業、可使時間) | 可能 | 不可能 | →×なら適用不可 | ||
2 | 手作業での計量・混合を行うか(発泡しやすく不適) | 行わない | 行う | →×なら適用不可 | |||
3 | 油面接着性は必須では無いか | ではない | 必須 | →×なら適用不可 | |||
4 | 接着剤の吸湿対策は可能か | 可能 | 不可能 | →×なら適用不可 | |||
5 | 金属接着の場合、プライマーの使用は可能か | 可能 | 不可能 | →×ならプライマーなしでの評価△ | |||
2液エポキシ | 共通 | 1 | 油面接着性は必須では無いか | ではない | 必須 | →×なら適用不可 | |
2 | 二液の扱いは可能か(計量・混合・塗布) | 可能 | 不可能 | →×なら適用不可 | |||
3 | 可使時間内での作業は可能か | 可能 | 不可能 | →×なら長可使時間タイプ△ | |||
長可使時間タイプ | 1 | 硬化時間は問題ないか | ない | あり | →×なら加温硬化△ | ||
加温硬化 | 1 | 硬化時間短縮のための加温は可能か | 可能 | 不可能 | →×なら適用不可 | ||
1液エポキシ | 加熱硬化タイプ | 1 | 低温保管は可能か | 可能 | 不可能 | →×なら適用不可 | |
2 | 加熱硬化は可能か | 可能 | 不可能 | →×なら適用不可 | |||
3 | 熱応力による問題は無いか | ない | あり | →×なら適用不可 | |||
プレミックスタイプ | 1 | 低温・冷凍での輸送・保管は可能か | 可能 | 不可能 | →×なら適用不可 | ||
2 | 油面接着性は必須では無いか | ではない | 必須 | →×なら適用不可 | |||
2液アクリル(SGA) | 共通 | 1 | 被着材表面はポーラスでないか | ではない | ポーラス | →×なら適用不可 | |
2 | 可使時間内での作業は可能か | 可能 | 不可能 | →×なら長可使時間タイプ検討△ | |||
3 | 臭気対策(換気)は可能か | 可能 | 不可能 | →×なら低臭気タイプ検討△ | |||
4 | 硬化収縮による問題はないか | ない | ある | →×なら低臭気タイプ検討△ | |||
5 | 未硬化のはみ出し部が密閉された空間内に置かれることはないか | ない | ある | →×なら低臭気タイプ検討△ | |||
2液型 | 1 | 二液の扱い(混合塗布、塗布後混合、重ね塗布、別塗布など)は可能か | 可能 | 不可能 | →×なら適用不可 | ||
プライマー・主剤型 | 1 | 接着層が1mm以上の部分はないか(硬化不良が生じやすい) | ない | ある | →×なら適用不可 | ||
2 | はみ出し部は硬化しにくいが問題ないか | ない | ある | →×なら適用不可 | |||
2液シリコーン | 共通 | 1 | 硬化阻害物質の問題は無いか | ない | ある | →×なら適用不可 →不明な場合は評価要△ | |
2 | 油面接着性は必須では無いか | ではない | 必須 | →×なら適用不可 | |||
3 | 二液の扱い(計量・混合・塗布)は可能か | 可能 | 不可能 | →×なら適用不可 | |||
4 | 硬化時間は問題ないか | ない | あり | →×なら加温硬化△ | |||
5 | 塗布装置の洗浄にトルエンやキシレンは使えるか | 使用可能 | 使用不可 | →×なら適用不可 | |||
加温硬化 | 1 | 硬化時間短縮のための加温は可能か | 可能 | 不可能 | →×なら適用不可 |
2. 候補接着剤の絞り込み
2-1. チェックリストの活用
表5-1の「消去法による接着剤の選定チェックリスト」で候補となる接着剤の種類が絞り込まれたら、「接着剤の選定・使用上の注意点、管理のポイントのチェックリスト」を用いて、細かい点をチェックしましょう。 表5-2には、一例として、一液湿気硬化型接着剤のチェックリストを示しました。他に、二液型エポキシ系接着剤、一液型エポキシ系接着剤、二液型ウレタン系接着剤、二液型アクリル系接着剤(SGA)のチェックリストがあります。
これらのチェックリストでは、選定・使用時の注意点のまとめと、管理項目、管理のポイントを、接着剤の受入・保管、接着作業の準備、接着作業、検査に分けて細かくチェックできるようになっています。特に重要なポイントは〇で示してあります。
接着作業では、チューブやカートリッジから直接塗布する場合、チューブやカートリッジからシリンジに詰め替えて使用する場合、ペール缶などから圧送塗布装置を用いて使用する場合など、使い方別にポイントが記載されています。
選定・使用時の注意点
- 空気中の水分と反応して硬化するため、作業時の環境湿度と温度により硬化速度が変化する。(低湿度時は加湿が必要)
- 水分を通さない大面積の接着では、内部まで硬化しない。
- シリコーン系接着剤は、硬化時にガス(酢酸、アルコール、オキシムなど)が発生する。
- オキシムは溶解性があるので、樹脂や未加硫ゴムでは要注意。
- アルコールは、メタノールを発生する物もあるので、大量使用での養生室などでは換気が必要。
- 電子部品や精密部品では、不純物の低分子シロキ酸が少ない電子部品グレードを使用すること。
- 変成シリコーン系の弾性接着剤でも硬化時に若干のガスが発生する。
- 空気加圧式塗布装置を用いる場合は、接着剤が直接空気に触れないようにプランジャーなどを入れること。
- 加圧空気は、水分を除去した乾燥空気を用いること。
- 変成シリコーン系の弾性接着剤はシリコーン系ではないので、高温では接着強度が低下する。
- 油面接着性は無いので接着面の脱脂を行うこと。
- 界面破壊する場合は、表面改質を行って凝集破壊にすること。(界面破壊ではせん断強度が高くても、剥離強度や耐久性は低く、ばらつきも大きい)
- 要求スペックに合ったグレードの選定は、接着剤メーカーと相談しながら行うこと。
表5-2 接着剤の選定・使用上の注意点、管理のポイントのチェックリスト(1液湿気硬化型接着剤)
※横にスクロールしてご覧ください。
工程 | 利点 | 管理項目 | 管理のポイント | |
---|---|---|---|---|
接着剤受入・保管 | 受入 | ロット管理 | 製造日の確認 | |
納入仕様書 | 試験結果の適合性確認 | |||
保管 | 〇 | 有効期限 | 未開封での期限を明記 | |
〇 | 保管場所・環境 | 特に湿度に注意、保管場所の温度・湿度を自動記録する(電池式) | ||
低温保管時の結晶化 | 結晶化温度以上で保管、庫内温度の自動記録(電池式) | |||
〇 | 吸湿 | 容器の密閉の確認 | ||
チューブやカートリッジは、乾燥剤を入れたポリ袋に入れて保管する | ||||
保管時の姿勢 | チューブやカートリッジ内の気泡を集めるため、ノズル側を上向きにして保管する | |||
工程 | 利点 | 管理項目 | 管理のポイント | |
接着作業の準備 | 作業場環境 | 〇 | 温度・湿度 | 許容温度・湿度の範囲を決める。温度を自動記録する。 |
低湿度時は加湿する。 | ||||
作業者 | 教育・訓練 | 事前実施、定期的に実施 | ||
安全・衛生 | 保護具を決めて配置する(手袋:かぶれ防止) | |||
〇 | 接着阻害物の移行の防止 | 保護クリーム、化粧品など。素手での作業禁止 | ||
接着剤取出し | 先入れ先出し | 間違わないシステムの構築 | ||
〇 | 開封までの放置時間(結露防止) | 低温保管の場合、室温に戻るまで密封状態で放置 | ||
〇 | 開封後の使用期間 | 新品の場合、使用可能期間を明記する | ||
接着剤の状態確認 | 分離・沈降の有無 | 有る場合は、容器の蓋をしたまま均一になるまで撹拌(水分を混入させないこと) | ||
色 | 限度見本で規定 | |||
粘度・流動性 | 簡易評価を実施 | |||
接着剤使用後の再保管 | 〇 | 容器内の空気の排除 | チューブやカートリッジ内の空気を押し出す | |
容器入りの場合は、液面にフィルムなどを浮かせて空気と遮断する | ||||
〇 | 容器の密閉 | 蓋周囲の清掃と蓋の密封 | ||
〇 | 冷蔵保管の適否(容器内での結露防止) | チューブやカートリッジ以外の容器の場合は、量が減って容器内の空気が多くなった状態で低温保管すると結露を起こすので、室温で保管する | ||
工程 | 利点 | 管理項目 | 管理のポイント | |
接着作業 | チューブやカートリッジから直接塗布する場合 | |||
脱泡 | 容器内の気泡等の除去 | チューブやカートリッジを上向きにして、容器内の空気等がなくなるまで押し出して捨てる。 | ||
チューブやカートリッジからシリンジに詰め替えて使う場合 | ||||
シリンジ等への充填 | 〇 | 気泡の巻き込み防止 | 空気を巻き込まないように、シリンジを上向きにして、チューブやカートリッジの口をシリンジの尻に押し当てて、接着剤をシリンジの下から上に徐々に押し込んでいく | |
〇 | プランジャーの挿入 | シリンジに詰めたらすぐに、空気を巻き込まないように、プランジャーを入れる | ||
〇 | 空気溜まりの排除 | シリンジを上向きにしたままプランジャーを押し込んで、シリンジの空洞部をなくす | ||
〇 | キャップ | シリンジの先端に密閉キャップを付ける | ||
〇 | 充填日、使用期限の記入 | 充填当日に使い切らない場合は、充填日時と使用期限をシリンジに明記する | ||
ペール缶などから圧送塗布装置を用いて使う場合 | ||||
脱泡 | 圧送タンク投入前か投入後に行う | |||
タンク内での沈降・分離確認 | 投入後時間が経過した場合に実施 | 目視またはヘラなどで確認 | ||
エア加圧式の場合 | 加圧エア | 乾燥空気を使用する | ||
接着剤へのエアの溶け込み対策 | 液面に浮かし蓋などでエアとの接触面積を減らす | |||
塗布ノズル | 〇 | ノズル内ゲル化 | アンチゲルタイマーの設定(夏期高温時基準) | |
〇 | 溶剤での洗浄 | 換気、引火対策(設備の防爆・準防爆)、衛生対策 | ||
溶剤洗浄後の乾燥 | エアでミキサー・ノズル内を乾燥させる | |||
塗布 | 塗布量 | 最適量と許容範囲を可視化しておく(限度見本) | ||
小物部品の場合は重量測定で塗布量を記録 | ||||
貼り合せ | 気泡混入 | 空気を巻き込まないように貼り合せる | ||
〇 | 可使時間 | 塗布開始から貼り合せ作業終了までの上限時間を規定しておく(夏期高温時基準) | ||
塗布に時間がかかる場合は、塗布開始からの経過時間をカウントし、アラームを出す | ||||
硬化までの加圧・固定 | 治具の清掃 | 接着剤付着などがないこと | ||
加圧力 | 部品の変形や位置ずれが生じず、接着層の厚さが所定厚さになる下限圧力程度 | |||
〇 | 二度加圧 | 空気の引き込みが生じやすいので二度加圧はしない | ||
室温での硬化 | 〇 | 温度・時間 | 最低温度・湿度と硬化時間の管理 | |
硬化場所の温度・湿度の自動記録 | ||||
低湿度時は加湿する | ||||
大量の養生を行う場合は、発生ガスに注意(換気) | ||||
工程 | 利点 | 管理項目 | 管理のポイント | |
検査 | 外観検査 | はみ出し部の硬化状態の確認 | ||
〇 | 抜取り破壊検査 | 凝集破壊率 | ||
未硬化部の有無 | ||||
強度と変動係数 |
これらのチェックリストでチェックして、十分な管理ができないと判断した場合は、その種類の接着剤の採用は避けた方が良いでしょう。何とかなるだろうで採用しても、いずれかの時点で必ず不具合に遭遇することになってしまいます。
2-2. 具体的な接着剤の選定を行う際の注意点
候補となる接着剤の種類が絞り込まれたら、接着剤メーカーに問い合せたり、カタログを見たりして具体的に候補品を選ぶ段階になります。
接着剤メーカーに問合せを行う場合には、候補となる種類の接着剤を扱っているメーカーに問い合せてください。希望する種類を扱っていない場合は、先のも述べたように、自社が扱っている他の種類の中から候補品を推薦されてしまい、思わぬ遠回りをさせられることになりかねません。問合せや打合せをする時には、「接着剤の選定・使用上の注意点、管理のポイントのチェックリスト」を活用して、疑問点を徹底的に解消しましょう。
3. カタログの見方
3-1.せん断強度とはく離強度の関係
接着強度の評価法として一般に広く行われているのは、引張りせん断試験とはく離試験です。図5-1は、接着剤の硬さ・伸びとせん断強度、はく離強度の関係を示した物です。接着剤の硬さ・伸びに対して、せん断強度とはく離強度は逆の関係になっています。はく離強が低いと壊れやすくなります。同じ接着剤であれば、温度が高くなると柔らかくなるので、横軸は温度と置き換えることもできます。 接着剤は、粘弾性という物質であるため、試験の引張り速度が変われば強度は変化するという特性があります。高速で引っ張ると硬い接着剤のような特性になります。また、接着層の厚さによっても強度は変化します。一般に、接着層が厚くなると、せん断強度は低下し、はく離強度は向上します。
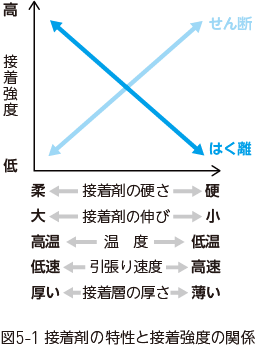
3-2. 接着剤のカタログは、せん断強度主体の記載
接着剤のカタログで示されている接着強度は、ほとんどがせん断強度で、はく離強度の記述はわずかしかないのがほとんどです。このため、どうしてもせん断強度で比較して選定することとなりますが、せん断が高い接着剤を選定すると、はく離強度が低い接着剤を選定している結果となり、はく離や衝撃などの局部荷重が加わると簡単に壊れてしまいかねません。
3-3. 両面テープ(粘着材)のカタログは、はく離強度主体の記載
両面テープなどの粘着材のカタログでは、ほとんどがはく離強度主体で書かれています。粘着剤は柔らかいので、はく離には強いですが、せん断方向の力や長時間力が加わり続けるクリープには弱くなります。両面テープを用いる部品組立においては、せん断方向に短時間に大きな力が加わる使われ方はほとんどないと思われますが、部品の自重が長期間にわたってせん断方向に加わっているという使われ方は多々あります。
また、反った状態の厚手のフィルムなどを両面テープで平面に貼付けるような使い方も多くあります。この場合は、フィルムが元の形状に戻ろうとするスプリングバック力がはく離方向に長期間にわたって加わっています。これらの状態では、時間と共に粘着剤がクリープを起こしてズレやはく離が生じます。このようなクリープ抵抗性は、保持力で表わされます。大半の両面テープのカタログには記載されていますが、保持力の記載のないものもあります。 両面テープの選定に当たっては、はく離強度より保持力の高い物を選定することが重要です。
3-4. 接着強度の温度特性は重要
接着剤でも粘着剤でも、温度が変化すると接着強度も変化します。接着部が曝される温度範囲での接着強度の確認を忘れてはなりません。
3-5. 強度データは参考程度に考える
3.1で述べたように、接着強度は種々の条件によって変化します。試験法が同じでも、メーカーによって試験の条件は異なります。接着剤でも両面テープでも、カタログに記載されている強度の数値は参考程度に考えなければなりません。強度よりも、本講座の第2回(http://www.macoho.co.jp/special/adhesive-seminar/principle-of-adhesion/)で述べた破壊状態(凝集破壊率)を確認することが重要です。
3-6. 耐久性データ
1)冷熱サイクル性は条件で大きく変化する
冷熱サイクルでの劣化は熱応力が原因ですが、熱応力や変形は被着材料の線膨張係数、組合せ、弾性率や厚さ、剛性、接着剤の弾性率、線膨張係数、厚さ、部品の構造や寸法など多くの要因で変化します。
カタログに記載されているデータは、引張りせん断試験片での結果が一般的ですが、実際の製品とは条件が大きく異なるため、実際の製品ではカタログの結果より大きく劣化することも少なくありません。カタログのデータは参考程度に留めて、決して設計データとして使わないようにしてください。
2)耐水性試験の結果は接着部の形状・寸法で大きく変化する
カタログには種々の耐久性試験の結果も記載されています。熱劣化は用いる被着材の材質によっても大きく異なります1)。耐水性や耐湿性は、図5-21)に示すように、引張りせん断試験片の重ね合せ長さ(ラップ長さ)が変わっただけで大きく変化します。カタログでの試験片より接着面積が大きい場合は、カタログデータより製品の劣化は少なくなりますが、製品の接着面積がカタログデータの試験片の面積より小さい場合は、より速く劣化することになります。
また、カタログと製品の被着材や表面処理が異なれば結果は大きく異なります。カタログのデータは参考程度に留めて下さい。
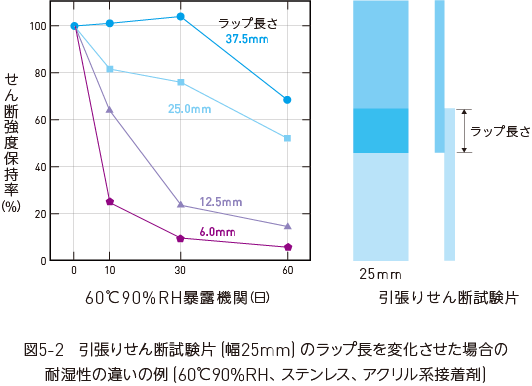
3)応力と水分の複合条件下では劣化が加速される
カタログの耐環境性試験は無負荷状態で実施されたものがほとんどです。応力耐久性として、疲労試験やクリープ試験の結果が記載されている場合もありますが、試験環境はせいぜい高温や低温などの空気中で行われています。図5-31)は、いずれも60℃環境でのクリープ破断試験の結果ですが、相対湿度を変化させています。湿度が高くなるとクリープ耐久性は急激に低下しています。
このように、応力と水分が複合されて加わると、応力や水分が単独で加わる場合に比べて急激に耐久性は低下します。疲労やクリープ耐久性のデータは、強度設計の参考値として用いられることが多々ありますが、水分の影響を考慮して低く見積もらなければなりません。
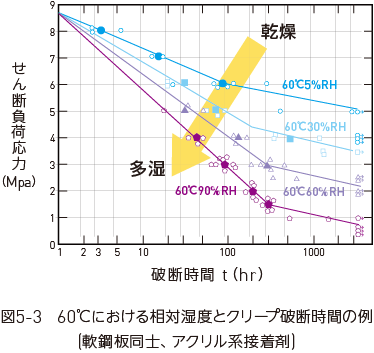
3-7. その他に確認すべきこと
1)硬化機構と影響因子
不思議なことに、接着剤のカタログには、その接着剤がどのような硬化反応で硬化するか、硬化に影響する因子としてはどのような物があるのかと言うことは詳しく書かれていません。硬化のメカニズムは接着プロセスに直接影響するし、接着剤の保存温度・保管期限にも大きく関係しています。この点が曖昧なまま使用して不良につながることは良くあることです。カタログに書いてなければ、必ずメーカーに問合せてください。
2)接着剤硬化物自体の物性
開発段階で、有限要素を用いて応力解析や変形解析を行うことは広く行われています。このためには、接着剤硬化物の弾性率と破断伸びの温度特性、ガラス転移温度(Tg)、線膨張係数などが必要となります。カタログに掲載されていないことも多いですが、メーカーに問い合せてデータを入手してください。
3)粘度
接着剤の粘度は重要です。カタログには室温での粘度は記載されていますが、温度を変化させた時の粘度はあまり掲載されていません。粘度は低温では高く、高温では低くなります。低温での粘度は塗布のし易さに影響するし、高温での粘度は、加熱硬化の時の染み込みや垂れにもつながります。 粘度は、接着剤のロットでかなり変化します。カタログに粘度の範囲が記載されていない場合は確認が必要です。塗布装置を用いる場合の条件設計や、浸透性・肉盛り性、隙間充填性、加圧力・接着層の厚さなどに影響します。 粘度の高さと垂れの少なさとは無関係です。高粘度でも時間の経過とともに徐々に垂れてしまうものや、低粘度でも垂直面で垂れないものも有ります。粘度の数字は、液体に加わる力の大きさで変化します。このような性質を揺変性(チキソトロピック性)と言います。液体に力が加わっている時は低粘度、力を抜くと高粘度となり、その粘度の比率が高いほど高チキソ性で塗布後には垂れにくいということになります。垂れ性や流動性が問題となる場合は、チキソトロピック指数をメーカーに確認してください。
4. 選んだ接着剤の適性を評価する
1)実際の材料・部品・工程での簡易評価
カタログを見て接着剤メーカーにも相談して候補接着剤を入手したら、細かいデータをとる前に、荒っぽくで良いので製品と同じ材質の被着材で、製品に近い形状の部品を用いて、実際の接着工程を想定したプロセスで接着作業を行い、性能評価をしましょう。試験片でデータを蓄積した後に、試作評価を行って、その時点で問題が見つかると、試験片での試験は無駄になってしまいます。
図5-4は、金属製パネル体のパネルと補強材の接着の評価試験の様子です。かなり荒っぽい評価をしているのが分かります。このような評価では、接着強度を数値で得ることはできませんが、必要なのは、接着後の部品に変形や機能上の問題が生じていないか、接着部にクラックが生じていないか、破壊試験では、簡単に剥がれてしまわないか、破壊面が凝集破壊になっているか、接着部に欠陥や変色、未硬化部は残っていないかなどを確認することです。
課題が見つかったら、表面処理法の検討や接着剤の改良や代替接着剤の選定を行います。
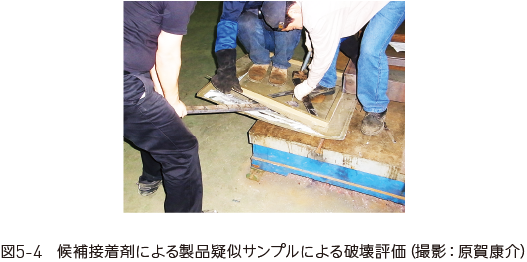
2)ダミーサンプルによる評価
実物に近い部品が準備できない場合は、図5-52)、図5-62)に示すような接着部のダミーサンプルでの評価でも結構です。ただし、被着材料、表面処理、接着プロセスなどは、実際にできるだけ合せた条件で行います。これらの例では、油が付着した状態で接着し、接着剤が硬化する前に接着剤の上からスポット溶接を行っています。
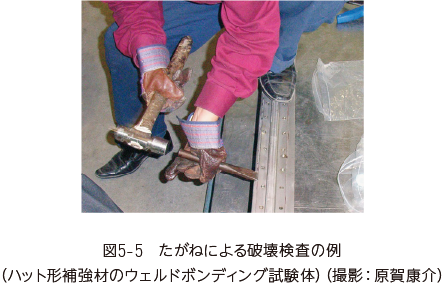
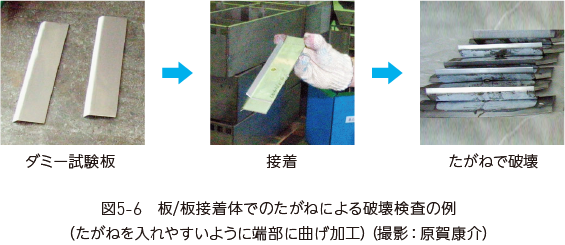
3)試験片でのデータの取得
大まかな予備試験で良好な結果が得られ、採用できる可能性が見えた接着剤については、各種の試験片を用いて詳細なデータ取得に移ります。試験片でデータ取得を行う場合に、JIS等の規格にこだわるケースが多々見られますが、規格にこだわる必要はないので、実際に使う被着材料を用いて、接着部の形状・寸法、力が加わる方向などを考慮して試験片を考案することが必要です。ガラスやセラミックスなどの割れやすい材料で、引張りせん断試験片やはく離試験片を作ってもガラスが割れてしまって接着特性の評価はできなくなります。
せん断力は、室温と高温下で、はく離強度は室温と低温下で測定しましょう。
次回は、設計、施工上の注意点について説明します。
参考文献
- ^ 原賀康介著:「高信頼性を引き出す接着設計技術-基礎から耐久性、寿命、安全率評価まで-」,日刊工業新聞社刊,(2013).
- ^ 原賀康介著:「分かる!使える!接着入門」,日刊工業新聞社刊,(2018).
著者紹介
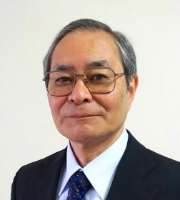
原賀康介 - (株)原賀接着技術コンサルタント
昭和48年(1973年)京都大学工学部工業化学科卒業、
同年 三菱電機(株) 入社、生産技術研究所、材料研究所、先端技術総合研究所に勤務
2007年より電気化学工業(株)に兼務出向
2012年3月三菱電機(株)および電気化学工業(株)を退任
2012年3月株式会社 原賀接着技術コンサルタントを設立し、各種企業における接着課題の解決へのアドバイスや社員教育などを行っている
1989年~1998年 自動車技術会 自動車構造接着技術特設委員会、構造接着技術特設委員会、構造形成プロセス専門委員会委員として、自動車の車体軽量化のための接着技術開発を実施
入社以来44年間にわたって一貫して接着接合技術の研究・開発に従事。
特に、構造接着技術と接着信頼性保証技術の開発に注力。