第7回 施工上の注意点
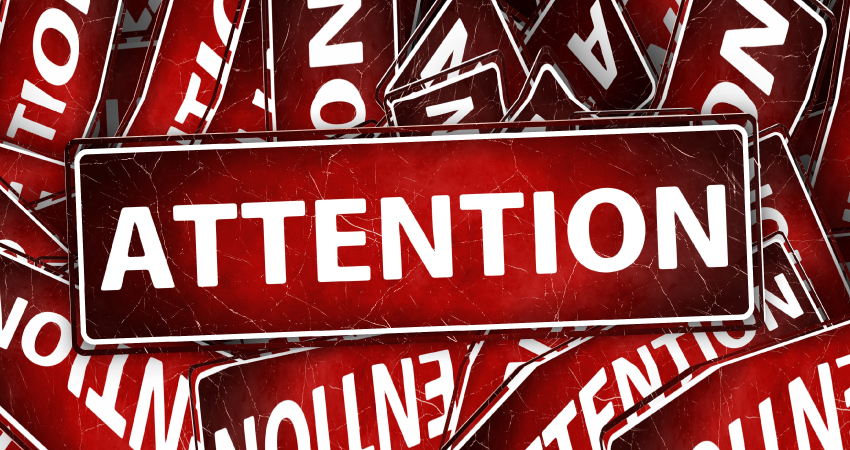
第7回は、施工上の注意点について説明していきます。
1. 特殊工程の作業と管理
1-1. 特殊工程の技術
「接着」は、特殊工程に区分されている技術です。
特殊工程とは、「その作業結果が後工程で実施される検査および試験によって、要求された品質基準を満たしているかどうかを十分に検証することが出来ない工程」と定義されています。要するに、最終工程の検査では性能・品質の良否を検査できないため、不良品を排除できない技術、工程、作業ということです。
1-2. 特殊工程で品質を確保するには
特殊工程の作業で品質を確保するためには、作業工程ごとに規定された許容範囲の条件内(公差内)で作業を行うことに尽きます。
作業者が、この程度は大丈夫だろうと規定された許容条件外の作業を行ってしまえば、後工程で不適切さを見つけることは困難になり、品質の悪いものができてしまうことになります。
1-3. 品質を担保する作業記録
最終工程で性能・品質の検査ができないとなれば、作業工程ごとに規定された許容条件内の作業がなされたということを担保していくしかありません。
そのためには、工程ごとの作業記録が重要になります。最終の検査工程では、作業ごとの記録をチェックして、全ての作業が許容条件の範囲内で行われたかどうかを確認します。出荷した製品が、フィールドで不良となった場合の原因究明にも工程ごとの作業記録がきわめて重要です。
作業記録は、作業者の手書きでは効率も悪いし記録の信憑性も問題となるので、検査・計測機器を用いて自動記録することが必要です。工程記録には、時刻も同時に記録しなければなりません。
2. 接着管理技術
2-1. 接着管理技術とは
「接着管理技術」とは、第6回で述べた「接着設計」の段階で規定された最適条件と許容範囲に従って適切な接着組立を行うために、組立現場において実施される検査や管理の技術です。接着される部品の状態、接着剤、作業環境などは時々刻々と変化しているので、接着工程ごとにその変化をいかに的確に捉えるかが、高い品質で効率的な組立を行う基本となります。
「接着管理」は実際の製造工程での管理ですが、「接着設計」が全て終了した段階から検討を始めるのではなく、「接着管理技術」と「接着設計技術」はコンカレントに相互にリンクして技術の作り込みをしていくことが必要です。
2-2. 接着管理技術の構成要素
接着管理技術は、図1に示すように、(1)部品管理、(2)材料管理、(3)工程管理、(4)設備管理、(5)検査・品質管理などの要素技術で構成されています。これらの要素技術は、独立して存在するものではなく、各要素技術は相互に強く関連しており、それらの強力な連携の元に接着管理技術は成り立っています。
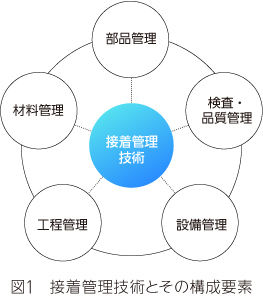
2-3. 各構成要素の実施内容
表1に、各構成要素の概要を示しました。
部品管理では、材料に間違いはないか、寸法は公差内か、接着面の状態は適切かなどのチェック法を決めます。 材料管理では、前処理から接着までの工程で用いる全ての材料が適切な状態かのチェック法を決めます。不適切状態の判定方法も必要です。
工程管理では、前工程までの作業は正しいか、規定された許容範囲内の条件で作業がされているか、実施した作業は適切だったかのチェック法を決めます。トラブル時の対応手順もこの段階で決めておきます。
設備管理では、設備・治工具・器具などが許容条件を超える要因を明確にし、管理する方法を決めます。 検査・品質管理は、最終工程での検査ではなく、各工程での操作・条件を数値化し、各工程にフィードバックする方法を決めます。教育・指導・訓練のプログラムも作成します。
要素技術 | 技術の概要 |
---|---|
部品管理 |
|
材料管理 |
|
工程管理 |
|
設備管理 |
|
検査・品質管理 |
|
3. 生産開始までに行うこと
3-1. 生産移行のための会議
表2には、生産開始までに行うことをまとめました。
まず、開発が終了したら、生産段階に移行するために、設計、生産技術、品質などの関係者が全員参加して生産移行会議を開催します。ここでは、接着設計で作り込まれた工程、条件で、要求仕様を満足できることを確認します。確認ができたら、工程ごとの細かい作業手順を具体的に決め、用具、治工具、設備の準備に入ります。併せて、作業環境の整備も行います。
項目 | 内容 |
---|---|
生産移行のための会議 |
|
作業手順を決める |
|
用具、治工具、設備の準備 |
|
作業環境の整備 |
|
工程管理表の作成 |
|
作業要領書の作成 |
|
トラブル時の対処方法の決定 |
|
現場責任者の教育・訓練 |
|
作業者の教育・訓練 |
|
3-2. 工程管理表、作業要領書の作成
まず、工程管理表を作成します。工程を決めて、工程ごとの要求仕様、作業のチェック項目、チェック方法、合否基準をまとめます。
次に、作業要領書を作成します。最適条件と許容範囲を明確に記載し、できるだけ分かりやすくビジュアルに作成しましょう。曖昧さをなくして、作業者に頼らない、作業者を困らせない書き方にすることが重要です。「綿棒が汚れたら交換する」、「プライマーを少量塗布する」、「接着剤を適量塗布する」、「接着剤の粘度が上昇してきたら」などの曖昧な表現を避けて、「綿棒は5個ごとに交換する」、「綿棒をプライマーに浸けた後、3枚重ねた新しいキムワイプに余分なプライマーを染みこませ、その綿棒を用いて接着面を一回だけこする」、「接着剤を1g塗布する」、「接着剤の混合開始から10分が経過したら」などと記述しましょう。
作業要領書には最適条件と許容範囲を明確に記載しますが、数値で示すだけではわかりにくので、例えば、二液型接着剤の配合比や混合度合いの表示では、最適条件、上限値、下限値を色や図・写真などでビジュアル化して掲載します。
3-3.トラブル時の対処方法を決める
発生する恐れがあるトラブルのパターンを考えられる限り掘り出し、それぞれについて対処方法を決めます。想定外のことまで想定しておきましょう。
いずれかの工程でトラブルが起こったら、ラインを停止しなければなりません。しかし、トラブルが生じた工程だけを止め、前工程を止めなければ問題が生じます。
図2は、一般的な接着工程において、ある工程でトラブルが生じた場合に、連動して停止させなければならない工程の範囲を示しています。例えば、加圧・固定の工程でトラブったら、表面処理や表面改質の工程から同時に停止させます。処理投入前の部品は投入しないように停止させます。表面処理や表面改質中の部品は処理を行い、処理終了後に停止させます。処理後の使用可能時間が上限を超えない時間でトラブルが解消できればそのまま流しますが、上限時間を超えた場合はラインから排除します。接着剤がすでに塗布された部品は、図3に示すように、接着剤の混合・塗布から貼り合せ・加圧固定までの時間が長くなると、接着強度が低下してしまいます。工程の最適条件と許容範囲で規定された上限時間を超えそうな場合は、接着剤を拭き取って、再洗浄を行う必要があります。
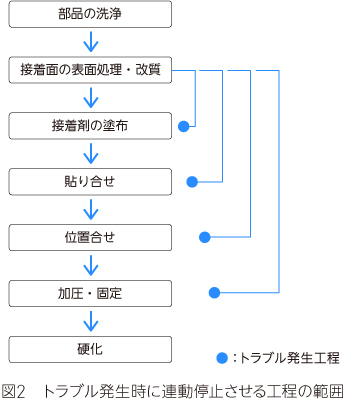
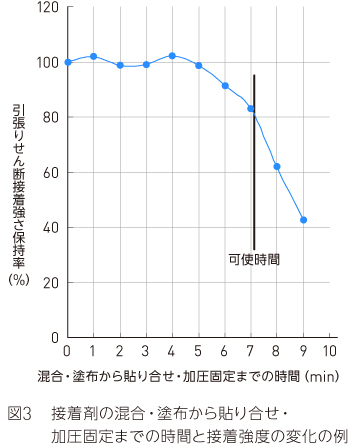
表面処理・表面改質の工程を停止させる場合、例えば、低圧水銀ランプによる短波長紫外線での表面改質では、ランプをONにして安定するまで時間がかかるため、工程が停止してもランプを消灯させてはいけません。塗布工程を停止させる場合は、塗布作業が待ち状態となるため、二液室温硬化型接着剤は塗布装置のミキサー内でゲル化や硬化を起こす心配があります。このため、塗布装置を自動的にゲル化防止モードでの運転に切り替える必要があります。このように、一つの工程内でもどこまで流すか、どこから止めるか、設備の運転状態をどうするのかなどを細かく決めておく必要があります。これらのことは、工程設計、設備設計の段階で決めておくことが必要です。 表面処理・表面改質の開始から加圧・固定までの間の工程中にある部品数は最小限に留めましょう。できれば、複数の工程をまとめて一つの工程に集約できれば、仕掛品を少なくすることができます。
3-4. 現場責任者の教育
接着設計段階で決められたプロセス、最適条件・許容範囲がなぜ指定されているかの理由を十分に理解し、トラブル時の対処方法まで繰返し訓練します。
3-5. 作業者の教育・訓練
指定された作業方法が必要な理由を理解させることは重要です。絶対にやってはならないこと、安全、衛生面での教育もしっかりと行って下さい。特に重要な工程では、有資格者作業とし、認定試験を行います。
4. 生産開始後の管理
生産が開始されたら、開発段階の接着設計・接着管理で決定された最適条件を目標に許容範囲(公差)内での作業を淡々と行えば良いように思いますが、接着される部品や、接着に用いるプライマーや接着剤、作業環境、設備、治工具の状態などは、時々刻々と変化しており、管理を怠ることは許されません。
4-1. 作業環境の管理
接着剤は、温度が低ければ硬化に時間がかかり、温度が高ければ硬化が早くなるため、作業場の温度管理が重要なことはよく知られています。しかし、湿度の管理も忘れてはなりません。瞬間接着剤、一液湿気硬化型の変成シリコーン系接着剤、シリコーン系接着剤、ウレタン系接着剤などは、湿度が低いと硬化に時間がかかります。また、二液型のウレタン系接着剤は、湿度が高いと発泡しやすくなります。図4は、海外のある工場内の温度と湿度の測定例です。温度の変化は、季節や昼夜の変化でほぼ予測できますが、1日の中でも湿度が大きく変わっていることが分かります。これでは、水分の影響を受ける接着剤での安定した接着は困難と言えます。 湿度は接着剤の硬化だけでなく、短波長紫外線や大気圧プラズマ処理などの表面改質後の接着性にも大きな影響を及ぼします。工場の始動時には安定した温度湿度になるように、始業の数時間前には空調を稼働させ、データロガーで温度・湿度を30分おきくらいの間隔で、自動記録させるようにしましょう。記録された結果を調整に反映させることも忘れてはなりません。
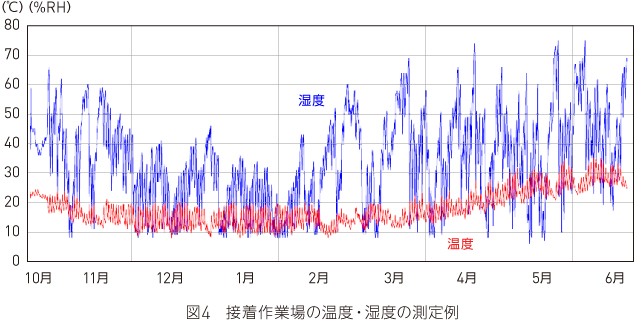
4-2. 設備・治工具の管理
接着剤の計量・混合・塗布装置は、長期間使用していると、接着剤の経路内にゲル化物や充填剤が付着や沈殿して管内抵抗が大きくなってきます。定圧圧送の場合は流量が低下し、流量制御されている場合は、管内の圧力が高まり、継目からの漏れや配管の破損につながります。パッキンも接着剤で膨潤して切れやすくなるため、定期的な分解掃除や交換が必要です。圧縮空気を用いる場合は、水、油セパレーターの管理も大切です。
接着の圧締治具や位置合せ治具に接着剤の硬化物が付着していては、図5に示すように、適切な作業ができなくなります。自動化で人手が入らない場合は、気がつくのが遅れる事があるので、付着しない対策や検知機器の設置が必要です。
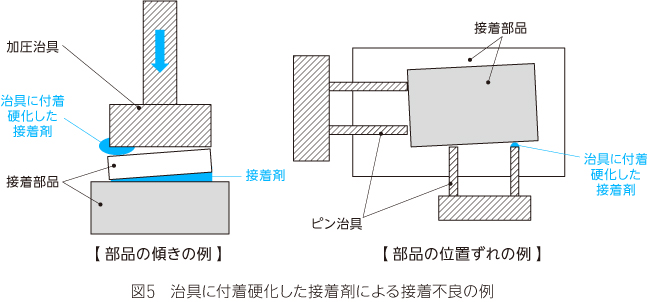
4-3.部品、接着前処理の管理
1) 部品の管理
部品を接着工程に流す前に、必ず材質が間違っていないかを、再度確認しましょう。 次に、部品の外観、寸法検査を行いますが、接着に影響するバリや局部変形などは、接着層の厚さに影響するため慎重に確認します。
2) 精度向上のための部品寸法のランク分け
接着層の厚さは内部応力や精度に大きく影響するため、接着層厚さの管理は重要です。表3は、軸と穴の接着において、クリアランス(接着層の厚さ)を、0.05~0.15mmに納めるために、部品の加工精度を上げないで、寸法でランク分けして組み合わせる例です。必要に応じて、このようなランク分けの作業を行います。
クリアランスの最適値 0.10
クリアランスの許容範囲 0.05~0.15
単位:mm
ケース | ランク分け | 軸外径寸法 | 穴内径寸法 | クリアランス (両側) | 最適値からの 最大ズレ (両側) |
合否 |
---|---|---|---|---|---|---|
ケース1 | なし (高精度加工) |
10-0.00-0.05 | 10+0.05+0.10 | 0.05~0.15 | 0.05 | 合格 |
ケース2 | なし (加工精度低減) |
10-0.00-0.10 | 10+0.00+0.10 | 0.00~0.20 | 0.10 | 不合格品 発生 |
ケース2-1 | ランク1 ランク2 |
10-0.00-0.05 10-0.05-0.10 |
10+0.05+0.10 10+0.00+0.05 |
0.05~0.15 0.05~0.15 |
0.05 0.05 | 合格 合格 |
ケース2-2 | ランク1 ランク2 ランク3 |
10-0.00-0.03 10-0.03-0.07 10-0.07-0.10 |
10+0.06+0.10 10+0.03+0.06 10+0.00+0.03 |
0.06~0.13 0.06~0.13 0.07~0.13 |
0.04 0.04 0.03 | 合格 合格 合格 |
ケース2-3 | ランク1 ランク2 ランク3 ランク4 ランク5 |
10-0.00-0.02 10-0.02-0.04 10-0.04-0.06 10-0.06-0.08 10-0.08-0.10 |
10+0.08+0.10 10+0.06+0.08 10+0.04+0.06 10+0.02+0.04 10+0.00+0.02 |
0.08~0.13 0.08~0.12 0.08~0.12 0.08~0.12 0.08~0.12 |
0.03 0.02 0.02 0.02 0.02 | 合格 合格 合格 合格 合格 |
3) キッティング、組合せ具合の確認
部品検査が終ったら、接着する部品を集めてキッティングします。ここで、接着部品の合い具合もチェックします。
4) 接着前処理
前処理を行った時刻は、以後の経過時間の判定に非常に重要なので、必ず記録しておきます。前処理が終った部品は、長時間滞留しないように、接着作業と同期させて行って下さい。
5) 表面改質の管理
短波長紫外線照射処理では、紫外線の照射強度を照度計で測定します。この時、波長にあった照度計を使わなければなりません。
接着剤を塗布する直前に、接着面の濡れ指数(表面張力)の検査を行います。36~38mN/mの濡れ張力試験液を現場に準備しておき、微量(直径数mm程度)滴下し、液が広がれば合格です。始業前、午後の始まり、部品や前処理のロットが変わるたびに測定します。検査した部品の表面は検査液が付着しているため、再度前処理工程に戻すか廃却します。
4-4.接着剤の管理
1) 接着剤の受入
接着剤メーカーや代理店から直接購入する場合は、出荷検査表の提出を義務づけて、受入時にデーターを確認して下さい。一液型エポキシ系接着剤など輸送中の温度に敏感なものでは、温度記録のデータロガーを同梱してもらい、高温に曝されていないかを確認します。 使用量が少なく市中の店舗で購入する場合は、製造日を確認して、新しいものを購入しましょう。一旦開封すると、使用期限が短くなるので、受入検査では、開封しての確認は避けます。受け入れた接着剤は、全容器に未開封での保管期限と開封後の使用可能期間を明記します。
2) 接着剤の保管
接着剤によって保管上限温度が異なるので、接着剤にあった温度で保管します。図6は、ある接着剤の保管温度・期間による粘度変化の一例です。40℃では短時間でゲル化しています。水分に敏感な接着剤は、できるだけ低湿度で保管します。保管庫の温湿度をデータロガーに記録し、定期的に確認します。規定の温湿度を超えたら、アラームがなるようにしておきます。温湿度のデータロガーは、停電でも停止しないように、電池式でなければなりません。
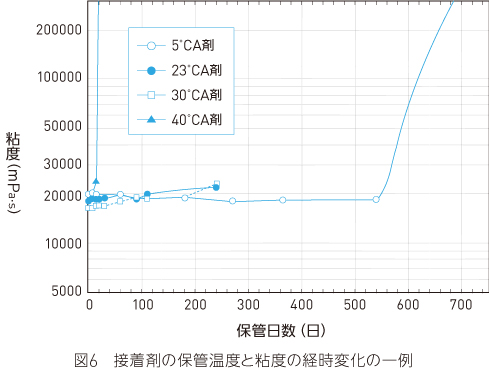
3) 接着剤の取出しと開封
冷蔵庫保管されている場合は、室温に取り出して、接着剤全体が室温に戻るまで開封してはいけません。低温で開封すると、接着剤が結露を起こします。取り出した接着剤は、必ず保管期限を確認します。保管期間が過ぎている物は、廃棄するか、検査を行って使用します。未開封の場合は、開封後の使用可能期日を記入します。一旦開封すると、保管期限内であっても、使用可能期間は短くなります。特に、湿気硬化型接着剤や低温保管が必要な接着剤は要注意です。保管中に分離しやすいものは、開封前に容器ごと撹拌して下さい。なお、追跡ができるように、接着剤のロット番号を記録しておきます。
4) 使用後の接着剤の再保管
使用が終ったら、すぐに容器に蓋をして密閉します。接着剤が少なくなって容器の空間が多くなっている場合は、再度の冷蔵庫保管は、容器の壁が低温になって、容器中の暖かい空気が容器内壁で結露を起こすので、避けましょう。
次回は、施工上の具体的な注意点について説明します。
著者紹介
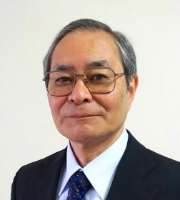
原賀康介 - (株)原賀接着技術コンサルタント
昭和48年(1973年)京都大学工学部工業化学科卒業、
同年 三菱電機(株) 入社、生産技術研究所、材料研究所、先端技術総合研究所に勤務
2007年より電気化学工業(株)に兼務出向
2012年3月三菱電機(株)および電気化学工業(株)を退任
2012年3月株式会社 原賀接着技術コンサルタントを設立し、各種企業における接着課題の解決へのアドバイスや社員教育などを行っている
1989年~1998年 自動車技術会 自動車構造接着技術特設委員会、構造接着技術特設委員会、構造形成プロセス専門委員会委員として、自動車の車体軽量化のための接着技術開発を実施
入社以来44年間にわたって一貫して接着接合技術の研究・開発に従事。
特に、構造接着技術と接着信頼性保証技術の開発に注力。