ウェットブラストの進化の物語 第8話
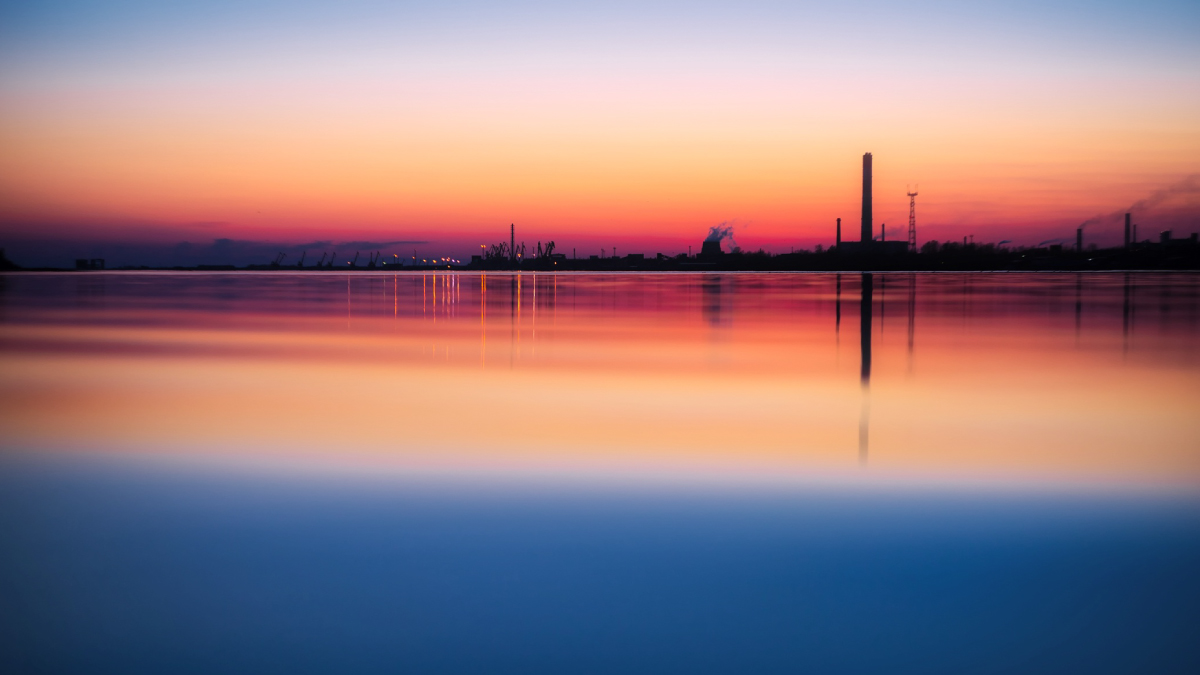
著:代表取締役/松原幸人
脱酸洗
酸洗は、金属加工におけるメジャーな工法です。
様々な用途がありますが、そのひとつとして、熱処理後の金属表面の「酸化膜の除去」に使われます。
一方、同じ処理にショットブラストが用いられる場合もあります。
しかし、ショットブラストは投射材のサイズが大きいため、処理後の表面凹凸も比較的大きなものになります。
大きな凹凸が残ったままでは製品化できないため、除去とは別に仕上げが必要となってしまい、工程がさらに一つ増えてしまいます。
なので、表面を一切傷めずに処理できる酸洗は、工程短縮の意味でも広く重宝されています。
(実際は、耐薬品性の高い素材や処理ムラへの対応で、酸洗は「やり直し」が度々発生し、作業工数は決して少なくないという見方もあるようですが)
そんな便利な酸洗ですが、決定的な問題があります。
「安全」です。
酸洗では、硫酸や塩酸などの危険な薬剤を用います。
そのため、設備、装備には厳重な安全対策が必須となります。
作業環境の安全対策ができていればそれで良いかと言えばさにあらず、処理後の排水や発生する中和スラッジの適切な処理も非常に重要となります。
それらを河川や排水溝に流出させた場合、重大な水質汚染を引き起こすからです。
前述したように、酸洗という工法自体はとても便利でメジャーな工法です。
酸性の液体に「つけるだけ」というシンプルさは、設備の構造もシンプルで済みますし、安価に大量生産を行う場合にはうってつけです。
しかし、酸洗は上に言った「安全」に対して大きな問題をはらんでおり、昨今しばしば目指すべき未来として取り上げられる「持続可能な社会」という点で考えた時、それは無視できないものでしょう。
当時、ステンレス研磨材による酸化スケール除去工法を確立していたマコーは、この酸洗に替わる工法開発に着手します。
それは、もう一方の代替工法であるショットブラストによる問題の解決も目的とする、新しい酸化被膜除去工法でした。
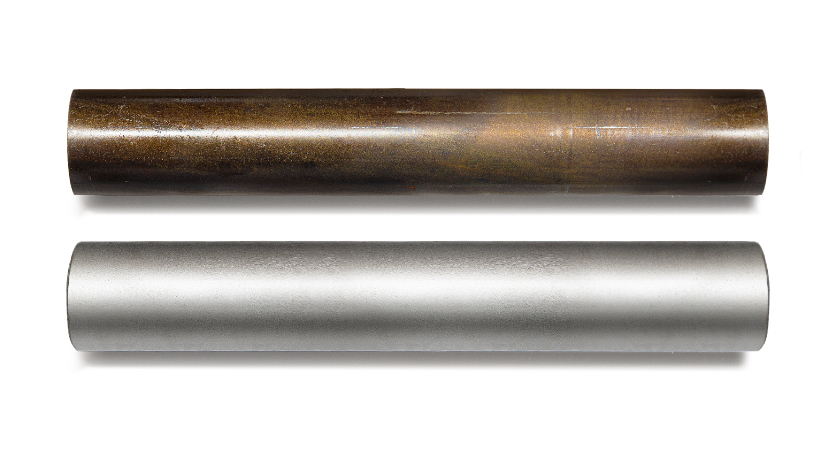
酸洗を脱する新しい工法。
その私たちの取り組みは、この後、前話でもご紹介させていただいた、「WLS(ウェットブラスト・ルブリカント・システム)として、脱ボンデと共に結実します。酸洗でもショットブラストでもない、安全かつ生産性の高い酸化被膜除去工法でした。
>冷間鍛造金型の寿命が2倍に伸びる潤滑下地処理(WLS)とは
安全面以外でも、ウェットブラストを用いた際の利点は多々ありました。
中でも「インライン化」が可能であった点は、生産性に非常に寄与するものでした。
また、極めて省スペースで設置が済むこと、ムラのない均一な処理が可能であること、研磨材残りも余計なダメージも極めて少ないこと、作業環境が良好であることなどが、多くの製造現場で評価され、設備導入が進んでいます。
マコーは、ウェットブラストに取り組むことを決めた当時から、「環境に優しい」という特長が、この工法の最大の利点のひとつだと考えていました。
社会にも、作業環境にも安心・安全であること。
それは、今後の世界のものづくりの中で、ますます重要な意味を持っていくように思います。
・・・
第8話「脱酸洗」、最後までお読みいただきありがとうございました。
第9話は「脱エアー」です。
他工法ではなく、ウェットブラスト自身の「問題」に関するお話です。